Tips for Improving Maintenance Work Order Management
Efficient maintenance work order management is crucial for ensuring smooth operations and maximizing asset uptime in any organization. Poorly managed work orders can lead to...
May 01, 2024
# of Minutes to Read
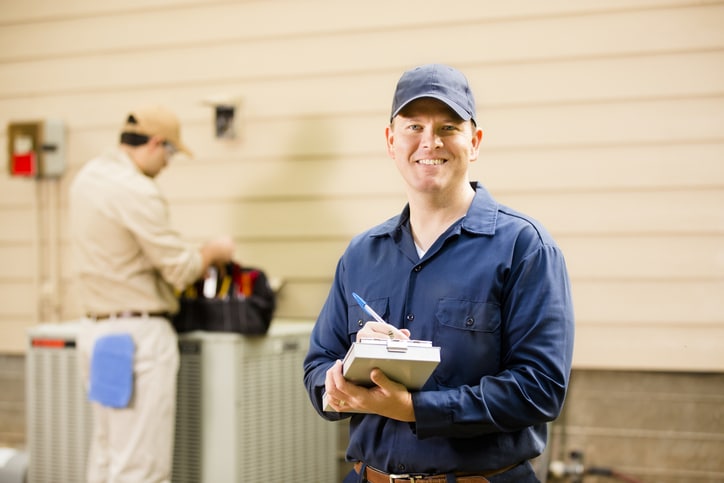
Efficient maintenance work order management is crucial for ensuring smooth operations and maximizing asset uptime in any organization. Poorly managed work orders can lead to delays, increased downtime, and ultimately, higher operational costs. In today’s competitive business environment, organizations cannot afford such inefficiencies, as they can severely impact productivity, customer satisfaction, and profitability.
Organizations often face several challenges when it comes to managing work orders effectively. These challenges may include a lack of centralized information, inefficient communication channels, lack of real-time visibility into work order status, and inadequate resource allocation. Without a streamlined process, work orders can easily fall through the cracks, leading to missed deadlines, duplicate efforts, and a backlog of maintenance tasks.
To address these challenges and improve work order management, this blog post will provide a comprehensive set of tips and best practices.
Implement a Centralized Work Order Management System
By implementing these tips and best practices, organizations can streamline their work order management processes, improve operational efficiency, and ultimately enhance their overall productivity and profitability.
One of the most significant challenges in work order management is the lack of a centralized system, leading to disorganized and siloed information. Implementing a centralized work order management system can revolutionize the way organizations handle maintenance tasks, ensuring efficiency and improving asset uptime.
A centralized system offers a single platform for creating, assigning, tracking, and closing work orders. This streamlined approach eliminates the need for disparate systems or manual processes, reducing the risk of miscommunication and lost or duplicated information. By consolidating all work order-related data in one location, maintenance teams, asset owners, and other stakeholders can easily access and share critical information, fostering collaboration and informed decision-making.
With RazorSync, businesses can seamlessly create, assign, track, and close work orders all from a single platform. This eliminates the cumbersome need for multiple systems or the hassle of manual tracking, thereby reducing errors such as miscommunication and the mishandling of work orders.
By integrating all work order-related data into one easy-to-access location, RazorSync not only simplifies the workflow for technicians on the ground but also enhances the transparency and efficiency of communication among maintenance teams, asset owners, and other stakeholders. This level of organization and accessibility ensures that everyone involved is on the same page, leading to improved collaboration and more informed decision-making.
When evaluating work order management software solutions, organizations should look for features that support their specific needs and requirements. Some essential features to consider include:
- Intuitive user interface: The system should be user-friendly, allowing maintenance teams and other stakeholders to easily create, update, and track work orders without extensive training.
- Mobile accessibility: With maintenance teams often working in the field, a mobile-friendly interface or dedicated mobile app can greatly enhance productivity and real-time updates.
- Customizable workflows: The ability to customize workflows and approval processes based on the organization’s unique requirements can streamline operations and ensure compliance with internal policies and regulations.
- Reporting and analytics: Robust reporting and analytics capabilities can provide valuable insights into maintenance operations, enabling data-driven decision-making and continuous process improvement.
Standardize Work Order Processes and Procedures
Establishing clear and consistent processes and procedures for work order management is crucial for ensuring efficiency, reducing errors, and fostering accountability across the organization. Standardization plays a pivotal role in streamlining communication, improving compliance, and enabling seamless collaboration among maintenance teams, asset owners, and other stakeholders.
Work order initiation is a critical first step in the process, and standardizing this step can help ensure that all relevant information is captured accurately and consistently. This includes details such as asset information, problem description, priority level, and any associated safety or operational risks. By creating templates or checklists for work order initiation, field service management organizations can reduce the risk of missing crucial details and ensure that maintenance teams have the necessary information to address the issue effectively. Discover how you can create custom templates using RazorSync.
Once a work order is initiated, the prioritization process becomes crucial. Standardizing prioritization criteria and procedures can help organizations effectively allocate resources and address critical issues promptly. This can be achieved by establishing clear guidelines based on factors such as asset criticality, operational impact, safety considerations, and regulatory compliance requirements. By following a consistent prioritization framework, organizations can minimize the risk of costly downtime or asset failures.
Leverage preventative maintenance strategies
Reactive maintenance, where assets are repaired or replaced only after a failure occurs, can lead to costly downtime, unexpected expenses, and increased safety risks. To mitigate these challenges, organizations should adopt a proactive approach by leveraging preventative maintenance strategies. Preventive maintenance involves routine inspections, servicing, and repairs aimed at identifying and addressing potential issues before they escalate into major failures.
By implementing preventative maintenance practices, organizations can minimize the need for reactive work orders, leading to numerous benefits. One of the most significant advantages is reduced downtime, as preventative maintenance helps identify and address potential issues before they cause disruptions to operations. This proactive approach not only ensures smoother operations but also extends the lifespan of assets, reducing the need for premature replacements and associated capital expenditures.
Moreover, preventative maintenance can lead to significant cost savings in the long run. While it may initially require an investment in resources and personnel, the costs associated with unplanned downtime, emergency repairs, and production losses can be substantially higher. By preventing these costly scenarios, organizations can optimize their maintenance budgets and allocate resources more effectively.
There are various preventative maintenance techniques that organizations can employ, tailored to their specific needs and asset portfolios. For example, scheduled maintenance which involves regular inspections, servicing, and replacements of components based on predetermined intervals, such as time, usage, or cycle counts. This approach helps ensure that assets are maintained before they reach a critical point of failure
Optimize work order scheduling and prioritization
Work order prioritization is a crucial step that should consider various factors, such as urgency, operational impact, safety implications, and resource availability. Organizations should establish a clear prioritization framework that takes into account these factors and aligns with their overall business objectives and priorities.
One effective strategy for prioritization is conducting a criticality analysis, which involves assessing the potential consequences of asset failure or downtime. This analysis can help organizations identify their most critical assets and prioritize work orders accordingly. Additionally, risk assessments can be performed to evaluate the likelihood and severity of potential risks associated with postponing or delaying maintenance activities.
Once work orders have been prioritized, efficient scheduling becomes paramount. This involves allocating resources, such as technicians, spare parts, and equipment, in an optimal manner to ensure timely completion of high-priority tasks while minimizing operational disruptions.
To optimize scheduling, organizations can leverage scheduling software or algorithms that consider factors like technician availability, skill sets, location, and travel time. These tools can help identify the most efficient resource allocation strategies and provide real-time visibility into the maintenance schedule, enabling proactive adjustments as needed.
Continuously Measure and Improve Performance
Continuously measuring and improving performance is a critical aspect of effective work order management. By regularly tracking and analyzing key performance indicators (KPIs), organizations can gain valuable insights into the efficiency and effectiveness of their maintenance operations, identify areas for improvement, and implement targeted corrective actions.
Establishing a robust performance measurement framework is essential for identifying bottlenecks, inefficiencies, and opportunities for optimization. Organizations should carefully select relevant KPIs that align with their operational goals and priorities. Some commonly used KPIs in work order management include:
- Work order completion times: Tracking the average time taken to complete work orders can help organizations identify potential delays or inefficiencies in the process. This metric can be further segmented based on work order type, asset criticality, or priority level to pinpoint specific areas that require attention.
- Backlog levels: Monitoring the number of outstanding or overdue work orders can provide insights into resource allocation and prioritization effectiveness. High backlog levels may indicate a need for additional resources or a review of the prioritization criteria.
- Maintenance costs: Analyzing the costs associated with maintenance activities, including labor, materials, and downtime, can help organizations identify opportunities for cost savings and optimize their maintenance budgets.
- Mean Time Between Failures (MTBF): This metric measures the average time between asset failures or breakdowns, which can be used to evaluate the effectiveness of preventive maintenance strategies and asset reliability.
- First-Time Fix Rate (FTFR): Tracking the percentage of work orders that are successfully resolved on the first attempt can help identify areas where additional training, documentation, or spare parts may be needed.
By implementing these tips, organizations can unlock numerous benefits, including increased productivity, reduced maintenance costs, improved asset reliability, and enhanced operational efficiency. Effective work order management not only minimizes downtime and disruptions but also contributes to overall profitability and customer satisfaction.
To further streamline and optimize work order management processes, organizations should consider leveraging field service management platform, like RazorSync. The powerful platform integrates various aspects of work order management, such as scheduling, dispatching, inventory management, and invoicing, into a single unified platform. Book a demo and experience an improved work order management for your field service company.